A folyékony fém elektronikai rendszere önállóan szereli össze saját magát.
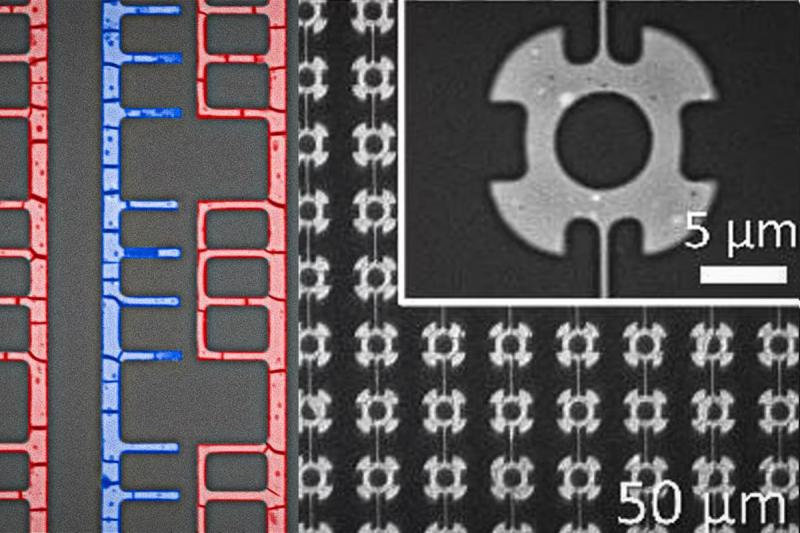
Csúcstechnológiai teljesítmény, de elérhető gyártási megoldásokkal - erről szól az elektronikai eszközök gyártásának az új, megdöbbentő módszere.
Az Észak-Karolinai Állami Egyetem kutatói egészen elképesztő gyártási technikát fejlesztettek ki, amely forradalmasíthatja a nanoméretű elektronikai eszközök előállítását. Az új "önszerelő" eljárás segítségével a csapat sikeresen készített el nanoméretű diódákat és tranzisztorokat, amelyek gyorsabb működést, alacsonyabb gyártási költségeket és nagyobb megbízhatóságot kínálnak a jelenlegi módszerekhez képest. Az eljárás során folyékony fémet és speciálisan kialakított öntőformákat használnak a bonyolult 3D-s szerkezetek precíz összeszereléséhez - számol be róla a New Atlas.
A Materials Horizons folyóiratban közzétett kutatás egy innovatív technológiát mutat be, amely az úgynevezett Field-fémek (indium, bizmut és ón folyékony ötvözete) felhasználásán alapul. Amikor ez a folyékony fém érintkezik a levegővel, egy vékony oxidréteg képződik a felszínén. A kutatók ezt a folyékony fémet egy egyedileg tervezett formához helyezték, amely szabadon alakítható és méretezhető a kívánt igényeknek megfelelően. Ezt követően egy különleges folyadékot öntöttek a fémre, mely negatív töltésű ligandum molekulákat tartalmazott. Ezek a molekulák képesek az oxidrétegből pozitív töltésű fémionokat "kivonni", amelyek később "építőkockaként" funkcionálnak. A folyadék a formán belül áramlik, miközben a fémionokat is magával vonzza. A forma kialakítása a kapilláris hatás révén irányítja az anyag mozgását, és segít abban, hogy ezek az építőkockák rendezett struktúrákat, például apró vezetékeket hozzanak létre. Martin Thuo, az NC State egyetem vezető kutatója és professzora hangsúlyozza, hogy ez a technológia új lehetőségeket nyit meg az anyagtudomány és a nanoelektronika területén, lehetővé téve a precíziós gyártást és az új funkcionális anyagok kifejlesztését.
"Öntőforma hiányában ezek a szerkezetek kaotikus és zsúfolt mintázatokat produkálnának. Azonban az öntőforma alkalmazásával precíz, szimmetrikus elrendezéseket lehet létrehozni."
Az összeszerelés végén az oldat elpárolog, ami elősegíti a szerkezetek további tömörödését. Ezt követően eltávolítják az öntőformát, majd az anyagot 600 °C-ra melegítik, hogy megszakítsák a ligandumok kémiai kötéseit. Ennek következtében a fémionok félvezető fém-oxidokká alakulnak, míg a ligandumokból származó szénatomok grafénrétegek formálódnak a vezetékek körül. Ezek a grafénbevonatok nemcsak a vezetőképességet növelik, hanem védelmet is nyújtanak az oxidáció ellen.
A kutatók a grafénrétegek átalakításával mutatták be a módszer sokrétűségét, hiszen ez lehetővé teszi a vezetékek elektromos jellemzőinek precíz optimalizálását is.
"Ez a módszer lehetőséget teremt arra, hogy a félvezetők sávszélességét a lehető legjobban kiaknázzuk, ezzel pedig fokozzuk a teljesítményüket."
- fűzte hozzá Julia Chang, a kutatás társszerzője és posztdoktori kutató.
A hevítés során fellépő enyhe zsugorodás ellenére a vezetékek sértetlenek maradtak, ami a módszer működőképességét bizonyítja. A csapat 44 nm-től 1000 nm-ig terjedő méretű szerkezeteket állított elő, amelyek versenyképesek a legkorszerűbb nanoméretű gyártási technológiákkal.
A hagyományos chipgyártással szemben, amely drága és gyakran hibás eredményeket produkál, ez az eljárás gyorsabb, olcsóbb és megbízhatóbb. A következő lépésként a kutatók összetettebb eszközök, például 3D-s chipek gyártásán dolgoznak, valamint a miniatürizálás további lehetőségeit kutatják.